
- Diy parallel port cnc controller how to#
- Diy parallel port cnc controller drivers#
- Diy parallel port cnc controller driver#
- Diy parallel port cnc controller software#
Hard Copies (a disk) of the downloadable content are available directly from a 3rd party.
Diy parallel port cnc controller software#
The Add-ons for Mill will only work with a licensed copy of Mach3 as this software is an Add-on, and not a stand-alone product. Simulation mode can be accessed by uninstalling (or not installing) the Parallel Port Driver. If a computer not connected to a machine is used to test code, please use Mach3 in Simulation mode – it will remove the 500 line limit. The community has created and tested many solutions. DIY solutions, or commercial solutions, follow the guide. They are many solutions, at all prices, but be careful : they are not all compatible with the software you use. Mach1, Mach2, and Mach3 may all be used on one computer, but only one version of each will co-exist on a single computer.Ī license is only required on the computer actually running a machine. CNC controller connects computer and stepper motors. For commercial users (anybody who uses the software to generate profit), we require a separate license purchase for each machine.

Non-commercial users (aka hobbyists) are permitted to use one Mach license for as many machines as they require.


Mill & Plasma: 500 line gcode limit (10,000,000 limit after licensing).While in Demo mode, the software has the following limitations: Without a license, Mach3 will operate in Demo mode. Mach3 CNC Control software will get you going. So I decided to piece together the methods that WORK into one single location so that folks like you and me can get their CNC machine working without having to sift through all the garbage (thousands of blogs and forums) to find out what works. I want to save you the pain of learning CNC the hard way like I did. The information I needed was scattered all over the place and I couldn’t find one solution that solved my problem. I searched everywhere on the web and I got really discouraged. It was frustrating back then, because I couldn’t find a PRACTICAL and FEASIBLE way to control my CNC machines on a hobby budget. When I built my first CNC Router it was finicky and unreliable and the software was a pain to work with.
Diy parallel port cnc controller how to#
I KNOW how to make a CNC machine work faster and more reliably, because I have spent years learning how. You want a solution that is proven and you don’t want to waste your time searching the web to find out how to use it. I am working on new project which is high voltage and high current 3 phase inverter module using IGBT.If you are here on this page now it is because you want to make your CNC machine work faster and more reliably.
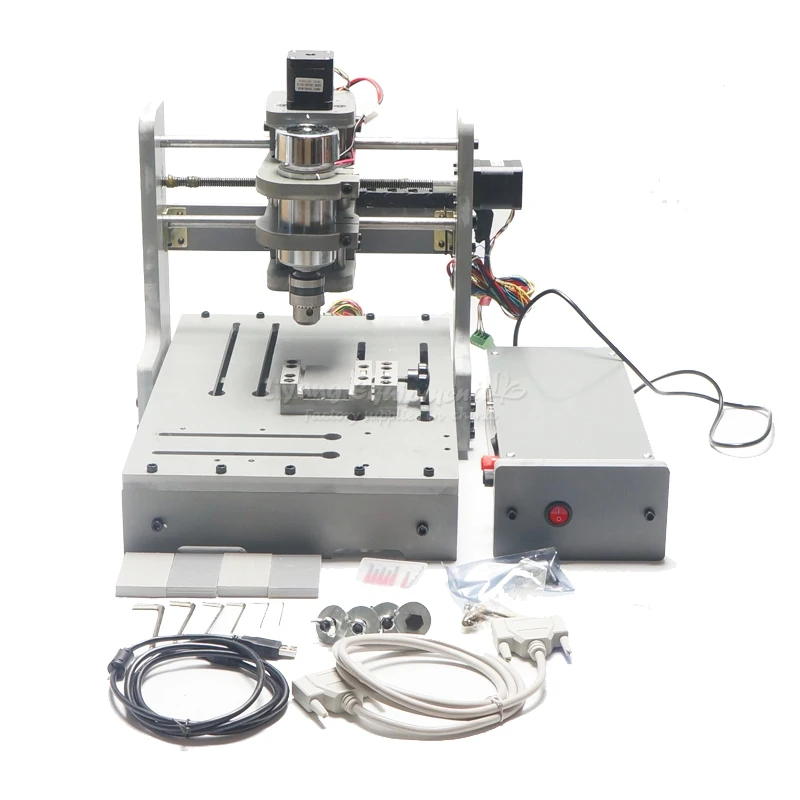
This unit comes with breakout board that can be configured for parallel control or optional USB-control.
Diy parallel port cnc controller driver#
You will still have a spare back-up driver for high-reliability, or use the spare for a rotary axis, and still be able to swap it over as a backup in case you have a driver failure in a high-reliability production environment. Have a machine with two motors driving the gantry? No problem.
Diy parallel port cnc controller drivers#
The Unit CNC Controller includes 4×4.2amp micro-stepping Bipolar Drivers at defaults, giving you versatility. This unit is expandable to your needs, versatile, and flexible. My 5 Axis CNC Milling _ CNC Router Controller_ Mach3_Mach4_UCCNC machine control softwareĥ Axis CNC Controller Box Mach3/Mach4, Bipolar Stepper Driver Based, USB/LPT This pre-wired 4Axis stepper motor control box has everything you need to drive a CNC Milling machine, CNC Router and motion control – with 4 stepper driver, one power supplies, e-stop, power plugs, limit switch, parallel port input or USB/LAN Optional. The SERVO Motion Control Board is maybe the fastest and lowest-cost way of getting your DC servo motor up and running
